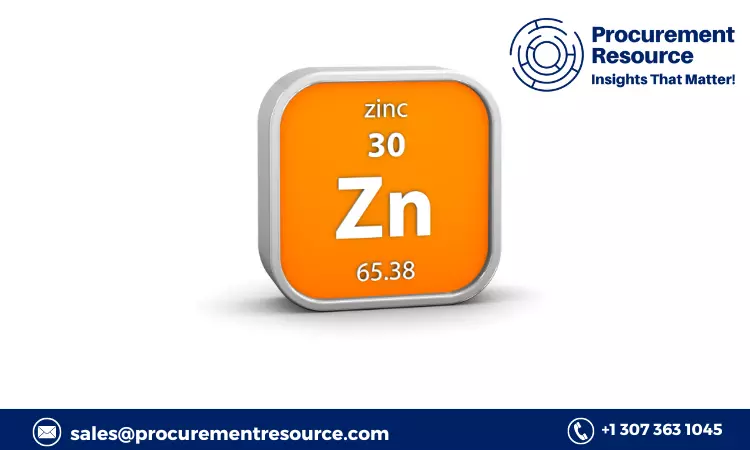
Zinc selenide (ZnSe) is a vital compound with a range of applications in optics, semiconductor devices, infrared optics, and laser components. It is valued for its unique optical properties, including high transmittance in the infrared spectrum and low absorption coefficient. Understanding the production costs associated with zinc selenide is essential for manufacturers, investors, and stakeholders involved in its production and utilization. This article explores the various factors influencing zinc selenide production cost and provides an in-depth analysis of the production process.
Factors Affecting Zinc Selenide Production Costs:
-
Raw Material Costs: The primary raw materials for zinc selenide production include zinc and selenium compounds. The prices of these raw materials can vary depending on factors such as market demand, supply chain disruptions, geopolitical tensions, and currency fluctuations. Fluctuations in raw material prices directly impact production costs and profitability.
-
Manufacturing Process: The production process of zinc selenide typically involves the reaction of zinc and selenium compounds at high temperatures in a controlled environment. The efficiency of the manufacturing process, energy consumption, equipment maintenance, and process yield significantly affect production costs. Investments in process optimization, automation, and energy efficiency measures can help reduce production costs.
-
Energy Costs: Energy consumption is a significant component of zinc selenide production costs, primarily during the high-temperature synthesis process. Energy prices, including electricity, natural gas, and fuel oil, influence overall production costs. Manufacturers may explore alternative energy sources, energy-saving technologies, and optimization strategies to mitigate the impact of energy costs on production expenses.
-
Labor Costs: Labor expenses associated with manufacturing, operations, maintenance, and quality control contribute to overall production costs. Labor costs vary depending on factors such as wage rates, workforce productivity, labor regulations, and workforce availability. Efficient workforce management, training programs, and productivity improvement initiatives can help optimize labor costs.
-
Capital Investments: Capital investments in production facilities, equipment, infrastructure, and technology upgrades impact upfront investment costs and ongoing operational expenses. Manufacturers may incur depreciation costs, financing expenses, and maintenance costs associated with capital assets, which are reflected in the overall production costs of zinc selenide.
-
Regulatory Compliance: Compliance with environmental regulations, health and safety standards, and quality control requirements may entail additional costs for manufacturers. Investments in pollution control measures, waste management systems, and regulatory compliance initiatives contribute to production costs. Non-compliance with regulations can lead to fines, penalties, and reputational damage, further impacting overall costs.
-
Economies of Scale: Production volume and economies of scale play a crucial role in determining production costs. Larger production volumes typically result in lower per-unit production costs due to efficiencies in raw material procurement, manufacturing processes, and overhead expenses. Manufacturers may explore strategies to increase production capacity, optimize resource utilization, and achieve economies of scale to lower production costs.
Request For Free Sample: https://www.procurementresource.com/production-cost-report-store/zinc-selenide/request-sample
Analysis of Zinc Selenide Production Process:
The production process of zinc selenide involves several key steps, including:
-
Raw Material Preparation: Zinc and selenium compounds are sourced and prepared for the synthesis process. These may include zinc oxide (ZnO) and selenium powder (Se) as primary raw materials.
-
Reaction and Synthesis: The raw materials are combined and subjected to a high-temperature reaction in a controlled atmosphere furnace. The reaction typically takes place in the presence of a flux material to facilitate the formation of zinc selenide.
-
Purification and Refinement: The synthesized zinc selenide undergoes purification processes to remove impurities and enhance its optical and chemical properties. Purification techniques may include recrystallization, vacuum distillation, or chemical treatments.
-
Shaping and Forming: The purified zinc selenide is shaped and formed into desired configurations, such as lenses, windows, prisms, or optical components. Machining, grinding, polishing, and coating processes may be employed to achieve the desired specifications.
-
Quality Control and Testing: The finished zinc selenide products undergo rigorous quality control and testing procedures to ensure compliance with specifications, performance criteria, and industry standards. Testing may include optical characterization, spectroscopic analysis, dimensional inspection, and durability testing.
Conclusion:
In conclusion, the production costs of zinc selenide are influenced by various factors, including raw material costs, manufacturing processes, energy expenses, labor costs, capital investments, regulatory compliance, and economies of scale. Manufacturers must carefully assess these factors and implement strategies to optimize production costs while maintaining product quality, reliability, and competitiveness. Understanding the intricacies of the zinc selenide production process and its associated costs is crucial for informed decision-making, strategic planning, and sustainable growth in the optics, semiconductor, and laser industries.
Contact Us:
Company Name: Procurement Resource
Contact Person: Leo Frank
Email: sales@procurementresource.com
Toll-Free Number: USA & Canada - Phone no: +1 307 363 1045 | UK - Phone no: +44 7537 132103 | Asia-Pacific (APAC) - Phone no: +91 1203185500
Address: 30 North Gould Street, Sheridan, WY 82801, USA