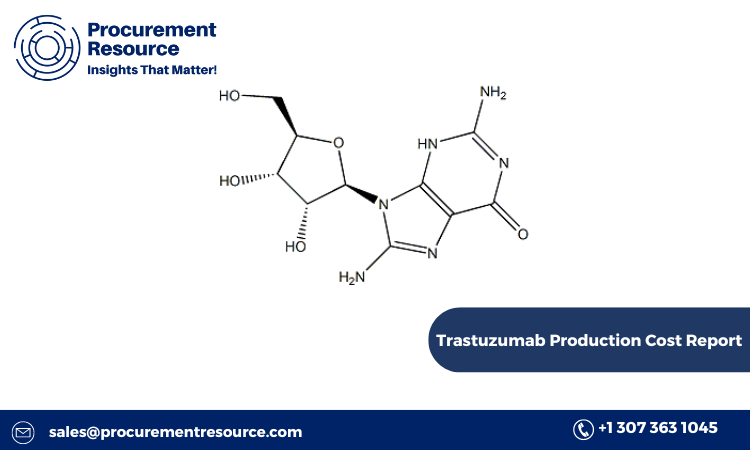
Trastuzumab, a monoclonal antibody used extensively in the treatment of HER2-positive breast cancer, represents a significant advancement in oncology. The production of trastuzumab is a complex and resource-intensive process, reflecting in its high cost. This blog provides a detailed analysis of the cost structure involved in producing Trastuzumab, encompassing various stages such as production process, manufacturing, raw material costs, and recent developments in the field.
Production Process
The production process of Trastuzumab involves several intricate steps, starting with the creation of the monoclonal antibodies. These antibodies are generated through recombinant DNA technology, where a gene encoding the desired antibody is inserted into a host cell, usually Chinese Hamster Ovary (CHO) cells. These cells are then cultivated in a controlled environment to produce the antibody in large quantities.
Request For Sample: https://www.procurementresource.com/production-cost-report-store/trastuzumab/request-sample
The production process includes:
- Cell Line Development: The first step involves the development of a stable cell line capable of producing Trastuzumab. This step is critical as it determines the yield and quality of the antibody. The cell line is created by introducing the Trastuzumab gene into the host cells, followed by selection and amplification.
- Fermentation: Once a stable cell line is developed, it is cultured in bioreactors under specific conditions to promote cell growth and antibody production. The fermentation process is closely monitored to ensure optimal conditions for the cells.
- Purification: After fermentation, the Trastuzumab is separated from the culture medium through a series of purification steps. This includes filtration, chromatography, and other techniques to ensure the antibody is free from impurities and contaminants.
- Formulation: The purified Trastuzumab is then formulated into a stable product suitable for therapeutic use. This involves adjusting the pH, adding stabilizers, and preparing the final dosage form.
- Quality Control: The final product undergoes rigorous quality control tests to ensure it meets all regulatory standards and specifications. This includes testing for purity, potency, and safety.
Manufacturing Report and Process
The manufacturing of Trastuzumab is conducted in state-of-the-art facilities that adhere to Good Manufacturing Practices (GMP). The process is highly regulated, and every stage requires strict compliance with international guidelines to ensure the safety and efficacy of the product.
The manufacturing process begins with the preparation of the culture media, which provides the necessary nutrients for the CHO cells. The media is sterilized and then used to cultivate the cells in bioreactors. The conditions in the bioreactors, including temperature, pH, and oxygen levels, are meticulously controlled to maximize antibody production.
Once the cells reach the desired density, the culture is harvested, and the Trastuzumab is extracted and purified. The purification process involves multiple steps, each designed to remove different types of impurities. This is a crucial stage, as the purity of the final product directly impacts its safety and efficacy.
After purification, the Trastuzumab is formulated and filled into vials or syringes under sterile conditions. The final product is then labeled, packaged, and stored under specific conditions to maintain its stability until it is administered to patients.
Raw Material Costs
The cost of producing Trastuzumab is significantly influenced by the raw materials used in the process. These materials include the culture media, reagents, and other consumables required for cell growth, fermentation, and purification. The cost of these materials can vary based on several factors, including the quality, source, and volume required.
- Culture Media: The media used to grow CHO cells is one of the most critical and costly components in the production of Trastuzumab. It must be rich in nutrients to support optimal cell growth and productivity.
- Reagents and Consumables: Various reagents are used throughout the production process, from cell line development to purification. These include enzymes, buffers, and chromatography resins, each contributing to the overall cost.
- Quality Control Materials: The materials required for testing the final product also add to the production cost. These include standards, reference materials, and testing reagents, all of which must meet stringent quality requirements.
- Packaging and Storage: The final product must be packaged in a way that ensures its stability and safety. The cost of packaging materials and the storage conditions required to maintain product integrity are also significant contributors to the overall cost.
Latest News
The Trastuzumab market has seen several developments in recent years, particularly with the introduction of biosimilars. Biosimilars are products that are highly similar to the original biologic drug but are typically less expensive. The approval of Trastuzumab biosimilars by regulatory authorities has introduced competition in the market, potentially reducing the cost of treatment for patients.
One of the major developments is the ongoing research and improvement in production technologies. Companies are investing in more efficient production processes, such as continuous manufacturing, which could lower production costs and increase the availability of Trastuzumab. Additionally, advancements in cell line engineering and purification techniques are being explored to enhance yield and reduce costs.
Moreover, the global expansion of production facilities is another significant trend. Leading pharmaceutical companies are establishing manufacturing plants in regions with lower operational costs, such as Asia and Latin America. This not only helps in reducing production costs but also ensures a steady supply of Trastuzumab to meet the growing demand.
In conclusion, while the production of Trastuzumab remains costly due to the complexity of the process and the high standards required, ongoing innovations and the introduction of biosimilars are likely to influence the future cost structure. The continuous improvement in manufacturing technologies and the expansion of production capabilities will play a crucial role in making this life-saving drug more accessible to patients worldwide.