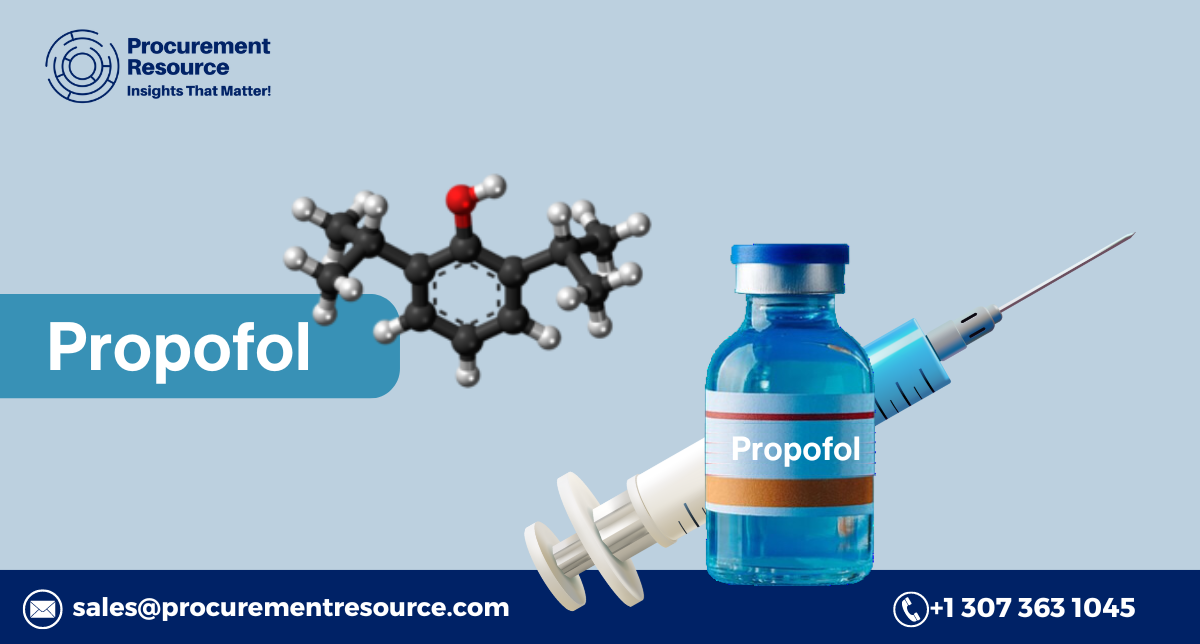
Propofol Production Cost
Propofol is a widely used anesthetic agent primarily employed for the induction and maintenance of general anesthesia, sedation for mechanically ventilated patients, and procedural sedation. Propofol is a short-acting drug that provides rapid onset of sedation, making it one of the most commonly used anesthetics in modern medicine. It is known for its ability to induce unconsciousness quickly and its short recovery time compared to other anesthetic agents.
Given the critical importance of propofol in various medical settings, understanding the production costs is essential for pharmaceutical companies, healthcare providers, and stakeholders. This article provides a comprehensive analysis of the factors influencing the propofol production cost, the manufacturing processes involved, and potential strategies for cost optimization.
Applications of Propofol
Propofol is widely used in various medical applications, such as:- General Anesthesia: Propofol is commonly administered during surgeries to induce and maintain general anesthesia.
- Sedation for Mechanically Ventilated Patients: It is often used for sedation in intensive care units (ICUs) for patients requiring mechanical ventilation.
- Procedural Sedation: Propofol is frequently administered for short medical procedures, such as endoscopy, colonoscopy, and minor surgeries.
- Day Surgery: Due to its rapid onset and quick recovery, propofol is favored in day surgeries where patients need to recover quickly and be discharged the same day.
Factors Influencing Propofol Production Costs
Several key factors contribute to the production cost of propofol, from raw material procurement to final formulation. Below are the main components affecting the cost:1. Raw Material Costs
Propofol production starts with the procurement of chemical raw materials. The cost of these materials can significantly influence the overall production cost.Active Pharmaceutical Ingredient (API)
Propofol’s chemical structure is 2,6-diisopropylphenol, and the synthesis of this API requires various reagents and intermediates:- Phenol Derivatives: The base molecule is derived from phenol, a relatively inexpensive and widely available chemical compound. However, its cost may fluctuate due to the prices of crude oil and petrochemical products.
- Solvents and Reagents: Organic solvents, catalysts, and reagents are required for synthesizing and purifying the API. Their costs can vary based on market demand and availability.
Excipients
Propofol is formulated in an oil-in-water emulsion for intravenous administration. The formulation contains:- Soybean Oil: This acts as the oil phase of the emulsion and can be influenced by agricultural factors and global commodity markets.
- Egg Lecithin: Used as an emulsifying agent to stabilize the oil-in-water mixture. Egg lecithin’s price can fluctuate depending on the availability of natural sources.
- Glycerol: Added to adjust the osmolarity of the emulsion.
- Water for Injection: High-purity water is required for formulating the emulsion, contributing to the overall production costs.
2. Manufacturing Process
The production of propofol involves several stages, each contributing to the total cost:Chemical Synthesis
The synthesis of propofol API involves several organic reactions, typically including Friedel-Crafts alkylation, followed by purification and isolation of the API. The steps include:- Synthesis Reaction: The initial reaction involves the alkylation of phenol with isopropyl groups using catalysts. The efficiency of this reaction impacts yield, which directly affects cost.
- Purification: After synthesis, the API undergoes multiple purification steps, including recrystallization or distillation, to achieve pharmaceutical-grade purity.
Formulation
After the synthesis of the API, propofol is formulated into an emulsion. The emulsion preparation involves:- Emulsification: Mixing the oil phase (soybean oil and propofol) with the water phase containing egg lecithin and glycerol requires specialized equipment, such as high-shear homogenizers, to create a stable formulation.
- Sterilization: As propofol is administered intravenously, stringent sterility requirements must be met. Sterilization processes like aseptic filtration or heat sterilization contribute to production costs.
3. Quality Control and Testing
Ensuring the safety, potency, and purity of propofol is crucial, given its use in anesthesia. Various tests are conducted throughout production:- Analytical Testing: Quality control involves testing for API content, emulsion stability, particle size distribution, sterility, and endotoxin levels. These tests require sophisticated equipment and highly trained personnel.
- Stability Studies: Long-term stability studies are required to ensure that propofol remains effective over its shelf life. These studies add additional costs in terms of time and resources.
4. Labor Costs
Labor costs play a significant role in propofol production:- Skilled Workforce: The production of propofol requires a skilled workforce, including chemists, formulation scientists, and quality control technicians. The costs associated with employing such professionals are significant.
- Training and Compliance: Employees must be trained in Good Manufacturing Practices (GMP) and other regulatory requirements, contributing to the overall labor costs.
5. Capital Investment and Equipment Costs
Establishing a production facility for propofol involves high capital investment:- Facility Construction: Building a facility that meets GMP standards for sterile drug production requires substantial investment.
- Specialized Equipment: Emulsification equipment, sterilization units, and aseptic processing facilities contribute to capital expenses. Regular maintenance and calibration of these machines are ongoing costs.
6. Regulatory Compliance
Regulatory compliance is a significant aspect of propofol production, particularly given its critical role in anesthesia:- FDA and EMA Approval: Obtaining approval from regulatory bodies such as the FDA (U.S.) or EMA (Europe) is a costly and time-consuming process involving clinical trials, documentation, and inspections.
- GMP Certification: Maintaining compliance with GMP standards necessitates continuous quality control measures, audits, and inspections, which add to production costs.
7. Energy and Utilities
Energy and utility costs are important considerations in propofol production:- Temperature Control: The synthesis and formulation of propofol often require precise temperature regulation, particularly in sterile environments, increasing energy consumption.
- Utilities: Water, electricity, and other utilities are necessary to run the production facility and maintain cleanroom environments, contributing to overall operational costs.
8. Packaging and Distribution
Once produced, propofol must be packaged and distributed to healthcare providers:- Packaging: Propofol is typically packaged in glass vials or pre-filled syringes. The choice of packaging material affects both the cost and the stability of the product.
- Storage: Propofol must be stored under specific conditions to maintain stability, adding to storage and warehousing costs.
- Distribution: Transportation costs, particularly for temperature-sensitive products, can also add to overall costs.
Estimated Cost Breakdown of Propofol Production
The production of propofol involves multiple stages, each contributing to the total cost. Based on these factors, a rough estimate of the cost breakdown is as follows:- Raw Materials: 20%-30%
- Labor Costs: 10%-20%
- Manufacturing Process: 20%-30%
- Quality Control and Testing: 10%-15%
- Capital Investment and Equipment: 10%-15%
- Regulatory Compliance: 5%-10%
- Packaging and Distribution: 5%-10%
Overall Estimated Cost
The estimated production cost of propofol typically ranges from $2 to $5 per vial (20mL of 1% solution). The exact cost can vary depending on the scale of production, raw material prices, and regulatory requirements.Strategies for Cost Optimization
To improve the cost-efficiency of propofol production, several strategies can be employed:- Feedstock Optimization: Sourcing cost-effective raw materials and negotiating with suppliers for bulk purchases can help reduce raw material costs.
- Process Optimization: Improving the efficiency of the synthesis and formulation processes can increase yields and reduce energy consumption, lowering production costs.
- Automation: Investing in automation technology can reduce labor costs and improve consistency in production, particularly in areas like emulsification and sterile processing.
- Scale-Up Production: Increasing production scale can help achieve economies of scale, reducing the cost per unit produced.
- Energy Efficiency: Implementing energy-efficient technologies and optimizing temperature control systems can lower utility costs.
- Regulatory Strategy: Streamlining regulatory approval processes and investing in early-stage compliance efforts can reduce delays and associated costs.
- Packaging Innovations: Exploring alternative packaging materials that are cost-effective while maintaining product stability can help reduce packaging costs.