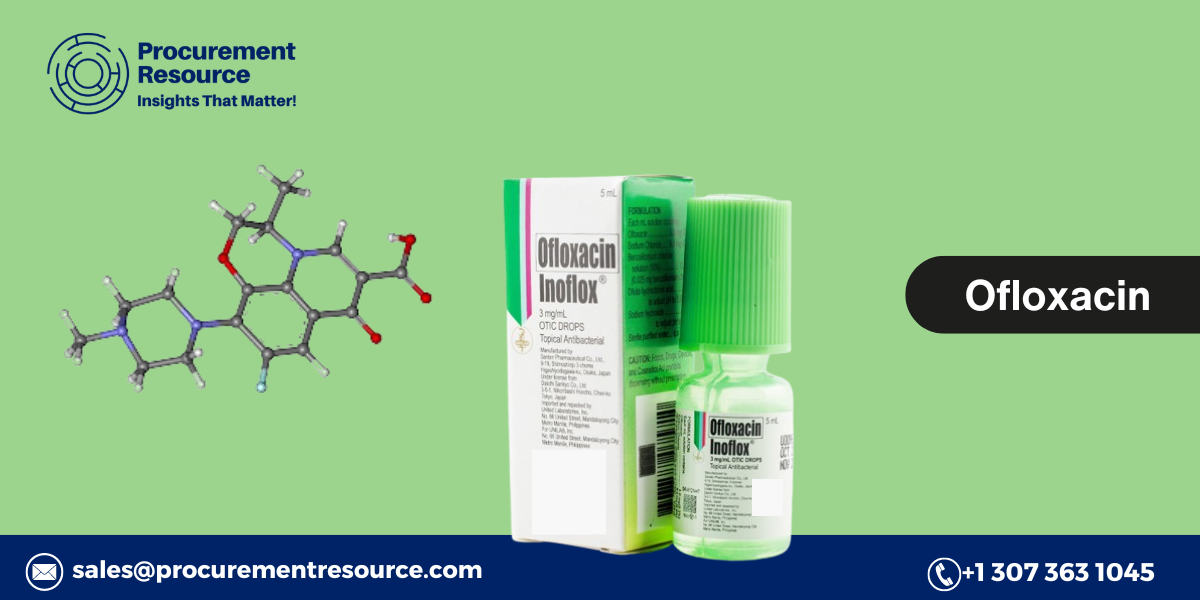
Ofloxacin Production Cost Analysis
In this article on ofloxacin production cost analysis would require extensive detail to cover the entire process and various cost factors involved. Here’s a breakdown of how I could structure the article for a comprehensive analysis.
Introduction to Ofloxacin
Ofloxacin is a synthetic antibiotic belonging to the fluoroquinolone class, commonly prescribed for treating bacterial infections such as respiratory infections, urinary tract infections, and skin infections. Since its introduction in the 1980s, it has become a staple in the pharmaceutical industry due to its broad-spectrum antibacterial activity.
This article provides a comprehensive analysis of the production costs associated with manufacturing ofloxacin. Factors influencing the cost include raw materials, synthesis process, technology, regulatory requirements, and environmental considerations.
Request For Free Sample: https://www.procurementresource.com/production-cost-report-store/ofloxacin/request-sample
Raw Material Costs
The production of ofloxacin begins with acquiring essential raw materials. The core structure of ofloxacin, a quinolone derivative, is synthesized through a series of chemical reactions involving various organic compounds. Key raw materials typically include:
- Starting materials like piperazine, acetic acid, and ethyl alcohol.
- Catalysts and reagents for facilitating reactions.
- Solvents for purification and isolation.
Fluctuations in raw material prices, influenced by supply-demand dynamics and geopolitical factors, can have a significant impact on the overall production cost. For instance, any disruption in the supply of basic chemicals can lead to cost increases.
Synthesis and Production Process Costs
The manufacturing of ofloxacin involves several key steps, including synthesis, purification, and formulation. Each stage carries associated costs:
- Synthesis: The process usually involves multiple stages, including the reaction of quinolone derivatives to form the core structure. These steps may require temperature-controlled environments, pressurized conditions, or other specific process requirements. This stage is labor-intensive and often demands a significant amount of energy.
- Purification: Once synthesized, ofloxacin undergoes rigorous purification to remove impurities. Filtration, crystallization, and other purification methods are implemented, all of which require additional equipment and resources.
- Formulation and Packaging: The final step involves the formulation of ofloxacin into a suitable form for administration, typically tablets or injections. This stage also includes packaging, labeling, and quality control.
Each of these steps carries its own cost considerations, including labor, equipment, maintenance, and overheads. Modern facilities with advanced automation can help reduce costs by minimizing labor requirements and improving efficiency.
Labor Costs
Labor costs constitute a substantial portion of the overall production cost of ofloxacin. Skilled professionals such as chemists, quality control personnel, and production operators are essential for ensuring product quality and compliance with regulatory standards.
Labor costs vary depending on geographical location, labor market conditions, and the level of expertise required. In countries with higher labor costs, manufacturers often seek to automate certain processes to reduce reliance on manual labor.
Equipment and Maintenance Costs
The production of ofloxacin requires sophisticated equipment, including reactors, filtration units, crystallizers, and other specialized machinery. Capital investment in these machines is a significant cost factor, and regular maintenance is necessary to prevent breakdowns and ensure consistent production quality.
Additionally, maintaining a sterile environment is essential for producing pharmaceuticals. Clean rooms, air filtration systems, and other equipment to control contamination are integral parts of a pharmaceutical production facility, contributing further to equipment-related costs.
Utility and Energy Costs
The energy-intensive nature of pharmaceutical production means that utility costs are a critical factor in determining the production cost of ofloxacin. Processes such as heating, cooling, and pressurizing demand substantial energy input. Utility costs may include:
- Electricity for powering equipment, lighting, and HVAC systems.
- Water for use in reactions, cleaning, and cooling processes.
- Gas for heating and fuel needs.
In regions with higher energy costs, production expenses increase accordingly. Implementing energy-efficient practices, such as optimizing reaction conditions or utilizing energy recovery systems, can help mitigate these costs.
Regulatory Compliance Costs
Compliance with regulatory standards is crucial in the pharmaceutical industry, particularly when producing antibiotics like ofloxacin. Meeting requirements from agencies like the FDA or EMA entails various costs related to quality control, documentation, and facility inspections.
- Quality Control: Rigorous testing is necessary to ensure that the final product meets purity, potency, and safety standards. Testing procedures such as High-Performance Liquid Chromatography (HPLC) or Mass Spectrometry (MS) require specialized equipment and trained personnel.
- Documentation: Compliance also involves extensive documentation and record-keeping, ensuring traceability of each batch produced. This process is essential for meeting Good Manufacturing Practices (GMP) and can add to labor and administrative costs.
- Inspections and Audits: Facilities may undergo periodic inspections by regulatory bodies. Preparing for and complying with these inspections can involve additional costs, such as fees for external consultants or temporary facility upgrades.
Non-compliance with regulatory requirements can result in penalties, production delays, and product recalls, all of which contribute to overall production costs.
Environmental and Waste Management Costs
Environmental considerations are increasingly important in pharmaceutical manufacturing, particularly for antibiotics. Proper disposal of waste and adherence to environmental regulations is essential to minimize the environmental impact of production processes.
- Waste Management: Chemical waste, solvents, and by-products generated during the synthesis and purification stages require appropriate disposal. Waste treatment facilities, chemical neutralization procedures, and safe disposal practices all incur costs.
- Emissions Control: Production facilities must manage emissions, including volatile organic compounds (VOCs) and greenhouse gases. Implementing emission control systems such as scrubbers and filters is necessary to meet environmental standards.
- Environmental Compliance: Some regions impose strict environmental regulations that necessitate additional investments in cleaner technologies, reducing waste and emissions. Failure to comply can result in fines or operational restrictions, which affect the overall cost structure.
Research and Development (R&D) Costs
The development of ofloxacin involves extensive R&D efforts to optimize synthesis routes, enhance yield, and reduce production costs. R&D expenses include salaries for research scientists, laboratory equipment, and the cost of materials used in experimentation.
Continuous R&D is also necessary for improving product quality, developing new formulations, and addressing emerging bacterial resistance. These ongoing R&D efforts contribute to the overall production cost and impact the competitiveness of the final product in the market.
Cost-Reduction Strategies in Ofloxacin Production
To stay competitive, pharmaceutical manufacturers often employ various cost-reduction strategies in the production of ofloxacin. Some common strategies include:
- Process Optimization: Streamlining the synthesis process by reducing reaction steps, improving yields, or using alternative, more cost-effective raw materials.
- Automation: Automating production processes can reduce labor costs and increase production efficiency. Advanced technologies, such as process analytical technology (PAT), enable real-time monitoring and control of critical parameters, minimizing waste and improving quality.
- Energy Efficiency: Implementing energy-efficient practices, such as using heat exchangers, optimizing reaction conditions, and investing in renewable energy sources, can help reduce utility costs.
- Sourcing and Supply Chain Management: Developing strategic partnerships with suppliers, negotiating bulk purchasing agreements, and reducing lead times can help minimize raw material costs.
- Recycling and Waste Reduction: Recycling solvents, reducing by-products, and optimizing waste management practices can reduce the environmental footprint and associated costs of production.
Contact Us:
Company Name: Procurement Resource
Contact Person: Leo Frank
Email: sales@procurementresource.com
Toll-Free Number: USA & Canada — Phone no: +1 307 363 1045 | UK — Phone no: +44 7537 132103 | Asia-Pacific (APAC) — Phone no: +91 1203185500
Address: 30 North Gould Street, Sheridan, WY 82801, USA