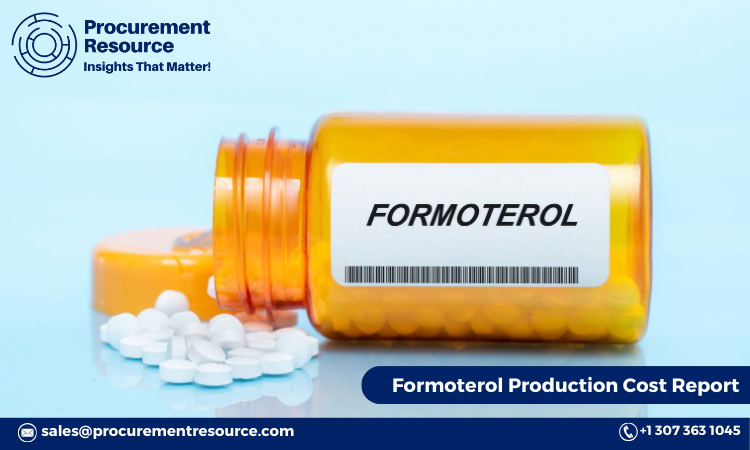
Formoterol, a highly effective bronchodilator, is a critical medication in the treatment of asthma and chronic obstructive pulmonary disease (COPD). As global demand for respiratory treatments continues to rise, understanding the production costs of formoterol has become essential for businesses in the pharmaceutical industry. Whether you are a manufacturer, a supplier, or a stakeholder involved in the procurement process, analyzing production costs can help optimize operations and enhance competitive positioning. This report offers a comprehensive breakdown of the factors affecting formoterol production costs and provides insights on how Procurement Resource’s cost analysis reports can be a valuable tool.
Why Formoterol Production Costs Matter
The production costs of formoterol influence pricing strategies, market competitiveness, and the overall profitability of companies in the pharmaceutical sector. Key elements driving formoterol production costs include raw material expenses, manufacturing technology, regulatory compliance costs, and labor. Here’s why these costs are crucial:
Request a Free Sample – https://www.procurementresource.com/production-cost-report-store/formoterol/request-sample
- Market Pricing and Competitiveness
Understanding production costs helps manufacturers set competitive pricing while maintaining profitability. With formoterol being in high demand due to the prevalence of respiratory issues, pricing can play a decisive role in market penetration and brand loyalty. - Supply Chain Optimization
Production cost analysis allows businesses to pinpoint areas within the supply chain that may be driving costs up unnecessarily. By understanding each component’s cost, businesses can renegotiate supplier contracts, consider alternative sources, or invest in more efficient manufacturing processes. - Resource Allocation and Budgeting
A clear view of production costs enables better financial planning and resource allocation, ensuring that companies maintain efficient spending practices. This becomes particularly important for companies with multiple products, as they balance investment across their portfolios. - Regulatory Compliance and Quality Control
In the pharmaceutical industry, adhering to stringent quality standards is mandatory, and regulatory compliance is non-negotiable. These requirements come with associated costs, making a detailed cost analysis essential for understanding how to maintain quality while managing expenses effectively.
Ask an Analyst – https://www.procurementresource.com/production-cost-report-store/formoterol/ask-an-analyst
The Power of Procurement Resource Formoterol Production Cost Reports
Procurement Resource provides specialized reports that dissect the production costs of essential products like formoterol. These reports offer an in-depth analysis of each cost component, providing invaluable insights for businesses aiming to streamline production and improve profitability. Key aspects covered in Procurement Resource’s Formoterol Production Cost Report include:
- Detailed Breakdown of Cost Components
The report categorizes and details all production-related expenses, including raw materials, labor, energy, transportation, and overheads. This granular breakdown enables businesses to identify where their spending is highest and to prioritize cost-reduction initiatives accordingly. - Raw Material Price Analysis
Raw materials often constitute a significant portion of the production cost. Procurement Resource provides analysis on raw material trends, including fluctuations due to geopolitical factors, natural resource availability, and market demand, helping businesses anticipate and manage risks. - Manufacturing Technology and Efficiency
Production efficiency is a direct contributor to cost savings. The report provides insights into the latest manufacturing technologies and practices that can improve efficiency, reduce waste, and lower costs, including recommendations for adopting environmentally friendly production practices. - Regional Cost Variations
Production costs can vary significantly across regions due to factors like labor rates, energy prices, and regulatory expenses. Procurement Resource’s reports highlight these variations, helping businesses make informed decisions about where to locate production facilities or source raw materials. - Labor and Energy Cost Trends
Labor and energy are recurring costs that can be highly variable depending on market conditions. The report provides an overview of trends in labor rates and energy costs, allowing businesses to understand how these elements affect overall production expenses.
How Procurement Resource Can Help You
Procurement Resource’s Formoterol Production Cost Reports are more than just numbers; they are a strategic tool that helps businesses enhance their procurement strategy, optimize supply chains, and ultimately boost profitability. Here’s how these reports add value:
- Supporting Informed Decision-Making
Armed with detailed cost data, businesses can make better-informed decisions regarding pricing, budget allocation, and resource planning. Understanding production costs allows companies to set prices that reflect both market expectations and profitability needs. - Strategic Supplier Negotiation
With insight into raw material costs and market trends, businesses can negotiate more favorable terms with suppliers. By knowing the price components in detail, companies gain leverage in discussions, leading to potential cost savings. - Identifying Cost-Saving Opportunities
By breaking down each element of the production cost, Procurement Resource enables companies to identify specific areas for cost reduction, such as switching suppliers, optimizing labor utilization, or adopting energy-saving technologies. - Enhancing Production Efficiency
The reports include recommendations for improving production efficiency and reducing waste, which can lead to significant long-term savings. Companies can leverage these insights to implement process improvements and streamline manufacturing operations. - Risk Management and Planning
Production cost reports from Procurement Resource include market forecasts and potential risks that could impact production expenses, such as raw material shortages or regulatory changes. This forward-looking approach allows companies to anticipate potential cost increases and plan accordingly. - Achieving Sustainability Goals
Many businesses today are focused on sustainability, and efficient production is key to achieving this. By identifying cost-saving measures that also reduce resource usage, these reports help companies move closer to their sustainability objectives, which is increasingly important in today’s market.
Request Your Free Sample Report Today!
If you are interested in gaining a competitive edge through cost transparency, Procurement Resource offers a free sample of its Formoterol Production Cost Report. This sample gives you a preview of the kind of insights that can help streamline your production process, improve cost efficiency, and make better business decisions. The free sample report provides an overview of:
Request Your Free Sample Report – https://www.procurementresource.com/production-cost-report-store/formoterol/request-sample
- Key Cost Components: Understand the most significant elements contributing to formoterol production costs.
- Market Trends and Forecasts: Gain insights into market trends that could impact production expenses.
- Cost Optimization Strategies: Explore actionable recommendations for cost savings and efficiency improvements.
Take the first step toward enhanced cost control and supply chain optimization by requesting your free sample today. Procurement Resource’s comprehensive Formoterol Production Cost Report is an indispensable asset for any business involved in the production, procurement, or distribution of formoterol.
In the competitive pharmaceutical landscape, understanding production costs is more than just a budgeting exercise—it is a strategic necessity. By gaining insight into the cost structure of formoterol production, businesses can make informed decisions, optimize spending, and secure a stronger position in the market. Procurement Resource’s production cost reports provide the data and analysis needed to achieve these goals, empowering companies to navigate cost pressures while maintaining high standards of quality and compliance. Don’t miss the opportunity to transform your cost management strategy. Request your free sample report today and unlock the power of data-driven decision-making.
Contact Us:
Company Name: Procurement Resource
Contact Person: Endru Smith
Email: sales@procurementresource.com
Toll-Free Number: USA & Canada - Phone no: +1 307 363 1045 | UK - Phone no: +44 7537171117 | Asia-Pacific (APAC) - Phone no: +91 1203185500
Address: 30 North Gould Street, Sheridan, WY 82801, USA