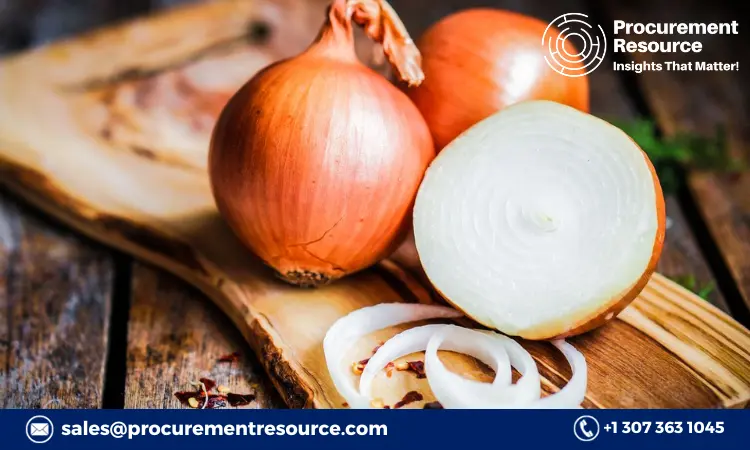
Dehydrated onion, a versatile ingredient with a wide range of culinary applications, is a staple in kitchens worldwide. Its production cost is a crucial consideration for manufacturers, as it directly impacts profitability and market competitiveness. Understanding the factors influencing the production cost of dehydrated onion is essential for businesses to optimize their production processes, pricing strategies, and overall operational efficiency. In this article, we delve into the intricacies of dehydrated onion production cost, exploring the key drivers, challenges, and strategies for cost optimization.
Overview of Dehydrated Onion Production:
Dehydrated onion production involves the dehydration or removal of moisture from fresh onions to extend their shelf life and enhance their flavor and aroma. The process typically includes cleaning, slicing, drying, and packaging of onions to produce dehydrated onion flakes, granules, or powder. Dehydrated onion products offer several advantages over fresh onions, including longer shelf life, easier storage and transportation, and convenience in handling and usage. They are widely used in food processing, seasoning blends, ready-to-eat meals, snack foods, and culinary applications.
Request For Free Sample: https://www.procurementresource.com/production-cost-report-store/dehydrated-onion-domestic/request-sample
Factors Influencing Dehydrated Onion Production Cost:
- Raw Material Costs:
The cost of raw onions is a primary component of dehydrated onion production cost. Fluctuations in onion prices, influenced by factors such as seasonal availability, weather conditions, market demand, and supply chain disruptions, directly impact production expenses. Variations in onion quality, size, and variety can also affect processing efficiency and yield, further influencing production costs. Price volatility in onion markets requires manufacturers to closely monitor market trends and establish effective procurement strategies to mitigate cost fluctuations.
- Labor and Overhead Costs:
Labor and overhead costs associated with dehydrated onion production, including wages, salaries, utilities, rent, and maintenance expenses, contribute significantly to production expenses. Labor-intensive processes such as onion cleaning, slicing, sorting, and packaging require skilled manpower and entail labor costs. Additionally, overhead expenses such as energy consumption, equipment depreciation, and facility maintenance add to the overall production cost. Implementing efficient labor management practices, optimizing production workflows, and investing in automation and technology can help reduce labor and overhead costs.
- Energy Costs:
Energy costs, including electricity, gas, and fuel expenses, constitute a significant portion of dehydrated onion production cost. Drying onions through dehydration processes, such as hot air drying or freeze-drying, requires substantial energy inputs. Fluctuations in energy prices, influenced by factors such as fuel prices, market demand, and regulatory policies, directly impact production expenses. Implementing energy-efficient technologies, optimizing drying processes, and exploring renewable energy sources can help mitigate energy costs and improve cost competitiveness.
- Packaging and Transportation Costs:
Packaging materials and transportation expenses contribute to the overall production cost of dehydrated onion products. Packaging materials, such as bags, pouches, or containers, are essential for preserving product quality, extending shelf life, and ensuring food safety. The cost of packaging materials, influenced by material prices, design complexity, and packaging volume, affects production expenses. Transportation costs, including freight charges, logistics fees, and fuel surcharges, impact the cost of delivering finished products to customers. Optimizing packaging designs, improving supply chain efficiency, and negotiating favorable transportation contracts can help manage packaging and transportation costs.
- Quality Control and Compliance Costs:
Quality control measures and compliance with food safety regulations entail additional costs for dehydrated onion manufacturers. Implementing stringent quality control protocols, laboratory testing, and sanitation practices are essential for ensuring product quality, safety, and regulatory compliance. Investments in quality assurance systems, staff training, and certification processes add to production expenses. However, maintaining high-quality standards is critical for building customer trust, ensuring product integrity, and mitigating risks associated with product recalls or regulatory non-compliance.
Strategies for Cost Optimization in Dehydrated Onion Production:
- Efficient Procurement Practices:
Implementing efficient procurement practices, including sourcing onions from reliable suppliers, negotiating favorable pricing contracts, and diversifying sourcing channels, can help mitigate raw material cost fluctuations.
- Process Optimization:
Optimizing production processes, streamlining workflows, and maximizing equipment efficiency can reduce labor and energy costs while improving production throughput and yield.
- Investment in Technology:
Investing in advanced drying technologies, automation systems, and energy-efficient equipment can enhance production efficiency, reduce energy consumption, and lower overall production costs.
- Supply Chain Management:
Optimizing supply chain logistics, minimizing inventory holding costs, and implementing just-in-time inventory practices can reduce packaging and transportation expenses.
- Continuous Improvement:
Embracing a culture of continuous improvement, fostering innovation, and leveraging data analytics to identify cost-saving opportunities and drive operational excellence.
Conclusion:
The production cost of dehydrated onion is influenced by a combination of factors, including raw material costs, labor and overhead expenses, energy costs, packaging and transportation costs, and quality control and compliance costs. Understanding these cost drivers and implementing strategies for cost optimization are essential for dehydrated onion manufacturers to remain competitive in the market. By adopting efficient procurement practices, optimizing production processes, investing in technology, and managing supply chain logistics effectively, businesses can enhance cost efficiency, improve profitability, and sustain growth in the dynamic and competitive dehydrated onion industry.
Contact Us:
Company Name: Procurement Resource
Contact Person: Leo Frank
Email: sales@procurementresource.com
Toll-Free Number: USA & Canada — Phone no: +1 307 363 1045 | UK — Phone no: +44 7537 132103 | Asia-Pacific (APAC) — Phone no: +91 1203185500
Address: 30 North Gould Street, Sheridan, WY 82801, USA