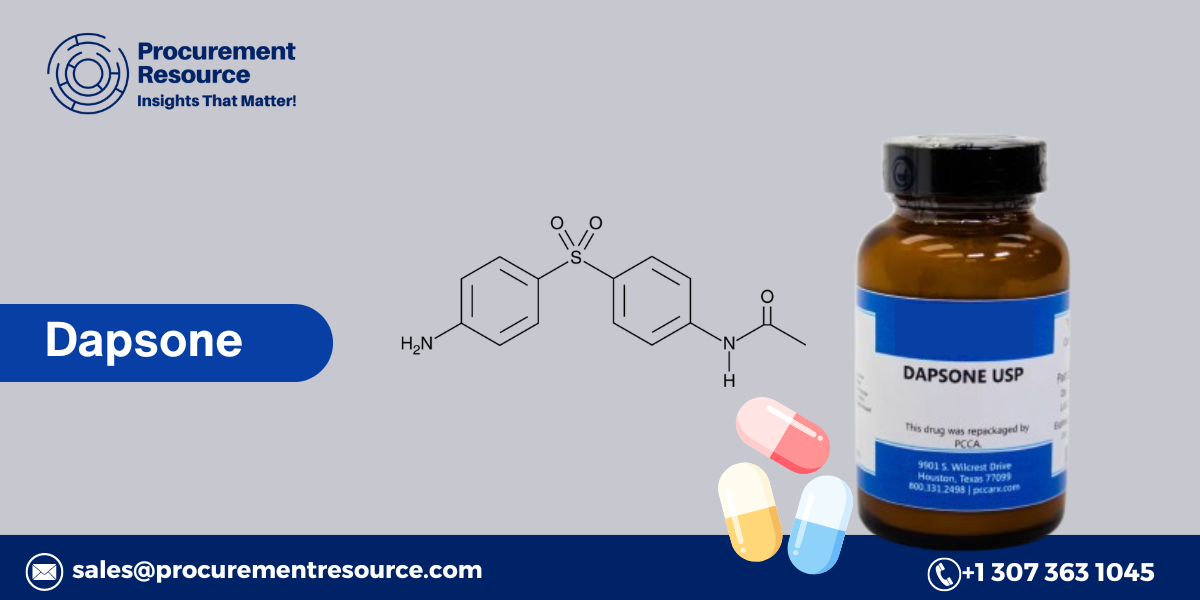
Dapsone Production Cost Analysis
Dapsone is an antibiotic that has been used for decades to treat a variety of infections and inflammatory conditions. It is primarily known for its role in treating leprosy (Hansen’s disease) and is also commonly used in the treatment of dermatitis herpetiformis, a skin condition related to celiac disease. More recently, it has found a place in dermatology, especially for acne and other inflammatory skin conditions. Understanding the dapsone production cost is essential for pharmaceutical companies, healthcare providers, and policymakers as they navigate issues of drug accessibility, affordability, and supply chain management.
This article provides an in-depth analysis of the different factors influencing dapsone production costs, from raw material sourcing and chemical synthesis to regulatory compliance and distribution. Each component has its distinct influence on the final cost of producing dapsone, and understanding these can help inform decisions in pharmaceutical manufacturing and pricing.
Key Factors Affecting Dapsone Production Cost
- Raw Materials and Chemical Synthesis
- Starting Materials: Dapsone is synthesized through a multi-step chemical process starting from simple aromatic compounds like aniline. The chemical name of dapsone is 4,4′-diaminodiphenylsulfone, which indicates its structural makeup as a sulfone derivative. The sourcing and cost of these starting materials, which are often derived from petrochemical processes, play a crucial role in determining the initial cost of dapsone production.
- Chemical Reagents and Catalysts: The synthesis of dapsone involves several steps, including nitration, reduction, and sulfonation. Each of these steps requires specific chemical reagents and catalysts to achieve the desired chemical transformation. For instance, nitration requires nitric acid, and the subsequent reduction step might use reducing agents such as hydrogen or metal-based catalysts like palladium. The price and availability of these reagents fluctuate depending on global market conditions, impacting the overall cost of production.
- Solvents: In many organic syntheses, solvents such as toluene, ethanol, or acetone are used to facilitate reactions or purify the final product. The cost of solvents, especially in bulk, is relatively low, but the cost of recovering and disposing of them adds to the environmental management costs in the production process.
- Yield and Waste Management: The yield of each chemical step directly influences production efficiency and cost. Low yields in any of the reaction steps can lead to higher raw material consumption and increased waste production. Waste management, particularly in the disposal of chemical byproducts, adds another layer of cost as facilities must adhere to environmental regulations.
- Manufacturing Process
- Chemical Synthesis Process: The manufacture of dapsone typically involves a multi-step chemical process. Each stage of this synthesis needs careful optimization to minimize waste, maximize yield, and ensure product purity. The precise steps include:
- Nitration of Diphenyl Ether: In this process, diphenyl ether is reacted with nitric acid to introduce nitro groups onto the molecule.
- Reduction: The nitro groups are subsequently reduced to amines using a reducing agent like hydrogen or metal catalysts such as palladium on carbon.
- Sulfonation: Finally, the resulting diamine compound is subjected to sulfonation, yielding 4,4′-diaminodiphenylsulfone, or dapsone.
- Equipment Costs: The chemical synthesis of dapsone requires specialized equipment like reactors, filtration units, and crystallizers. Equipment that can withstand harsh chemicals and high temperatures is necessary, particularly for the nitration and reduction stages. High initial capital investment is required to set up these manufacturing processes, which is amortized over the life of the production facility. Maintenance and replacement of this equipment also add to operational costs.
- Energy Costs: Manufacturing pharmaceuticals, particularly through chemical synthesis, requires significant energy inputs. For example, maintaining the high temperatures needed for reactions or running purification processes such as distillation or crystallization requires continuous energy usage. Energy costs can vary based on geographic location, with regions relying on renewable energy sources potentially benefiting from lower costs in the long term.
- Chemical Synthesis Process: The manufacture of dapsone typically involves a multi-step chemical process. Each stage of this synthesis needs careful optimization to minimize waste, maximize yield, and ensure product purity. The precise steps include:
- Labor and Operational Costs
- Skilled Labor: The production of pharmaceuticals like dapsone requires highly skilled chemists, chemical engineers, and quality control experts. These professionals oversee each step of the process, from reaction optimization to final product testing. The cost of skilled labor varies depending on the country where production takes place, with higher wages in developed countries contributing significantly to overall production costs.
- Facility Operation and Maintenance: The ongoing costs of running a pharmaceutical manufacturing facility include not just labor but also utilities (electricity, water, etc.), routine maintenance of equipment, and overhead expenses like facility security, waste management, and administration. Facilities operating under Good Manufacturing Practice (GMP) guidelines must maintain strict cleanliness and operational standards, further increasing operational costs.
- Regulatory Compliance
- Good Manufacturing Practices (GMP): Pharmaceutical companies must adhere to strict regulatory guidelines, such as GMP, which are enforced by agencies like the U.S. FDA or the European Medicines Agency (EMA). Compliance with GMP includes maintaining clean production environments, implementing quality control measures, and ensuring product consistency. Meeting these standards adds to production costs as companies must invest in regular audits, facility inspections, and quality assurance protocols.
- Quality Control and Testing: Every batch of dapsone produced must be subjected to rigorous testing to ensure it meets the required purity, potency, and safety standards. Quality control testing, including methods such as High-Performance Liquid Chromatography (HPLC) and mass spectrometry, is essential for confirming that the drug is free from impurities or contaminants. The equipment and skilled personnel needed for these tests increase the overall production cost.
- Regulatory Filing and Approval Costs: Before a pharmaceutical product like dapsone can be marketed, it must undergo regulatory review and approval in each country where it will be sold. The cost of filing these applications, along with the costs associated with conducting clinical trials and submitting documentation, can be considerable, especially when entering new markets.
- Packaging and Distribution
- Specialized Packaging Requirements: Pharmaceuticals like dapsone require packaging that ensures product stability and protects against environmental factors such as light, humidity, and temperature. The packaging materials, including blister packs, bottles, and tamper-evident seals, must meet strict regulatory standards, further increasing the cost.
- Cold Chain Logistics (if applicable): Although dapsone generally does not require cold storage, other specialized pharmaceuticals often do. For such drugs, cold chain logistics (maintaining a specific temperature range during transportation and storage) are critical to ensuring the product’s efficacy. Even without cold storage, ensuring safe and secure transportation of pharmaceutical products adds to the logistical cost of distribution.
- Distribution and Retail Markup: The distribution network for pharmaceuticals, from manufacturer to pharmacy or hospital, includes wholesalers and distributors, each adding a markup to the price. These additional costs must be considered in the overall pricing model for dapsone and other pharmaceuticals.
- Research and Development (R&D)
- Development of Generic vs. Branded Dapsone: The production cost for generic dapsone is typically lower than that of a branded version, as the latter may involve significant investment in research and clinical trials for approval. Generic manufacturers benefit from not having to replicate the original development work. However, developing a new formulation or delivery mechanism for dapsone, such as a topical or controlled-release version, would involve significant R&D expenditure.
- Clinical Trials and Safety Studies: For branded dapsone products or new formulations, the cost of conducting preclinical and clinical trials to demonstrate safety and efficacy can be substantial. These trials require coordination with healthcare providers, recruiting volunteers, and gathering data over extended periods, which adds significantly to the cost.
- Environmental and Waste Management Costs
- Waste Treatment: The synthesis of dapsone produces chemical waste that must be properly treated and disposed of in compliance with environmental regulations. The cost of waste management is increasingly relevant, particularly in regions with strict environmental controls. Proper waste treatment facilities, along with the disposal of hazardous materials, add to the operational expenses.
- Sustainability Initiatives: As global regulations and public demand push for more sustainable manufacturing processes, pharmaceutical companies may invest in greener practices, such as reducing energy consumption, minimizing waste, and utilizing renewable raw materials. These sustainability efforts can initially increase production costs but may offer long-term savings and regulatory advantages.
Breakdown of Dapsone Production Costs
- Raw Materials (Aromatic compounds, reagents): 20-30%
- The cost of basic chemical feedstocks and reagents, which are derived from petrochemical sources and refined to produce high-purity starting materials.
- Labor and Operational Costs: 15-25%
- Skilled labor and general operational expenses, including utilities, facility maintenance, and administrative costs.
- Energy Costs: 10-15%
- Costs associated with the energy required to power manufacturing processes such as chemical reactions, filtration, and purification.
- Regulatory Compliance and Quality Control: 10-20%
- Compliance with GMP, as well as costs related to quality control testing, documentation, and regulatory filings.
- Packaging and Distribution: 5-10%
- Packaging materials, distribution logistics, and secure