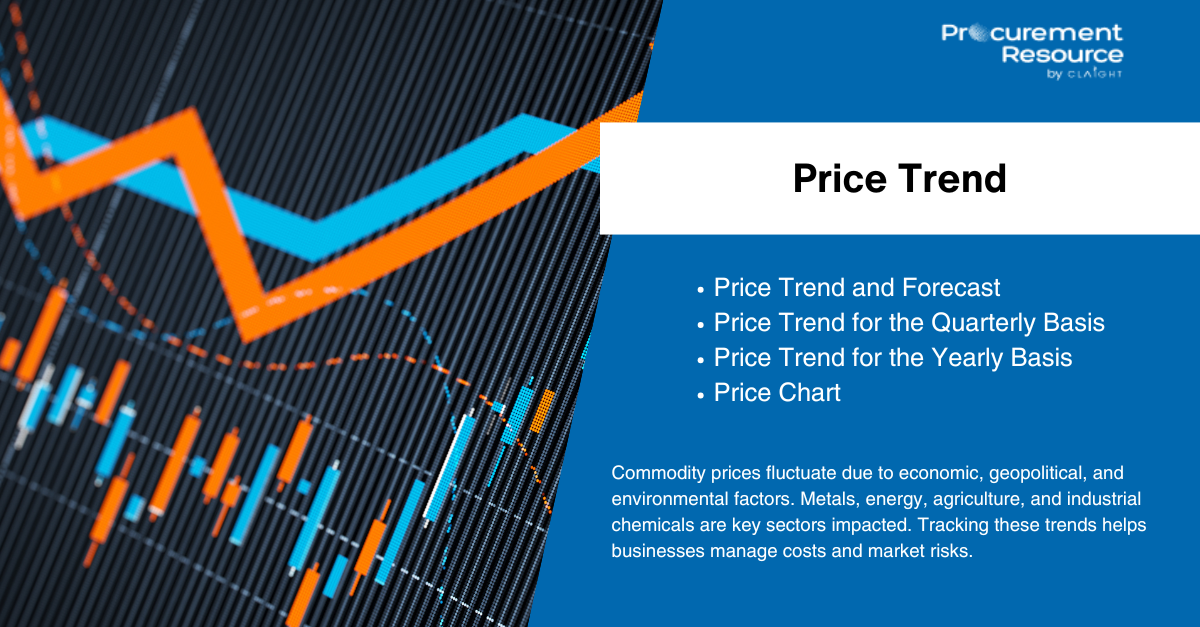
Potassium Stearate Manufacturing Plant Project Report
The construction of large warehouses plays a pivotal role in the logistics, distribution, and e-commerce industries. These structures are essential for companies that handle large volumes of goods, ensuring efficient storage, sorting, and dispatching processes. As global demand for e-commerce and consumer goods continues to grow, the need for these expansive structures is on the rise. However, understanding the construction costs of large warehouses has become more complex due to a variety of factors, including material prices, technological advancements, labor costs, and environmental considerations.
This article explores the factors influencing the of Large Warehouses Construction Cost Trend, the current trends in the industry, and the key considerations that builders, developers, and businesses must keep in mind when embarking on warehouse construction projects.
Factors Influencing Warehouse Construction Costs
Before diving into the current trends, it’s crucial to understand the key factors that influence warehouse construction costs. These factors vary by region, the scale of the project, and the specific requirements of the business.
1. Location and Site Conditions
One of the most significant factors influencing construction costs is the location of the warehouse. Building in urban centers or areas with high real estate demand typically incurs higher land costs. Additionally, if the site is challenging—such as uneven terrain, poor soil quality, or high water tables—the cost of preparing the site for construction can increase substantially. These conditions may require additional groundwork, such as land grading, foundation stabilization, and the installation of specialized drainage systems.
2. Warehouse Size and Layout
The size and layout of the warehouse directly impact its cost. Larger warehouses require more materials, longer construction timeframes, and additional labor. Additionally, the complexity of the layout—such as the need for specialized areas like cold storage or high-tech sorting systems—will also affect the total cost. Custom designs or non-standard layouts can lead to higher expenses due to the need for specialized labor or equipment.
3. Materials and Labor Costs
The price of construction materials fluctuates over time based on supply and demand dynamics. In recent years, the construction industry has seen price volatility due to global supply chain disruptions, particularly in materials like steel, concrete, and timber. The cost of labor is another crucial factor, and this can vary greatly depending on the region, the availability of skilled workers, and the complexity of the warehouse’s design.
Steel is commonly used in warehouse construction due to its strength, durability, and cost-effectiveness. However, any rise in steel prices or a shortage in steel supply can lead to a significant increase in the cost of constructing steel-frame warehouses. Other materials such as insulation, roofing systems, and flooring can also add up, depending on the warehouse’s specific requirements.
Enquire For Regular Prices: https://www.procurementresource.com/resource-center/large-ware-house-distribution-centre-construction-cost-price-trends/pricerequest
4. Technology and Automation
The increasing demand for technologically advanced warehouses, particularly those employing automation and robotics, has led to a rise in construction costs. Automated systems, conveyor belts, robotic arms, and state-of-the-art material handling systems require specialized infrastructure, which can add considerable costs. Furthermore, data centers or high-tech control rooms might need to be incorporated into the design, further increasing the overall cost of construction.
5. Energy Efficiency and Sustainability
Sustainability and energy efficiency are becoming key considerations in warehouse construction. With growing concerns about climate change and energy consumption, more companies are opting for warehouses that are energy-efficient, utilizing renewable energy sources such as solar panels or wind turbines. While these green technologies often come with higher initial costs, they can significantly reduce long-term operational costs, making them a worthwhile investment. Additionally, environmentally friendly materials, such as recycled insulation or sustainable building practices, can further raise the upfront cost of construction.
Current Trends in Large Warehouse Construction Costs
The construction of large warehouses has evolved in recent years due to shifts in industry demands, technological innovations, and changing economic conditions. Below are some of the key trends that are influencing warehouse construction costs today.
1. Increased Demand for E-Commerce and Distribution Centers
The growth of e-commerce, fueled by the rapid rise of online shopping, has significantly increased the demand for large distribution centers and fulfillment centers. Companies like Amazon, Walmart, and other major retailers are investing heavily in large-scale warehouses to meet consumer demand for quick delivery times.
This trend has led to an increase in the construction of more advanced warehouses, often featuring automated systems for order picking, sorting, and packaging. The construction of these high-tech facilities often comes at a higher cost, as they require specialized design and infrastructure.
2. Shift Toward Multi-Story Warehouses
In urban areas where land is limited and expensive, there has been a shift toward multi-story warehouses. Rather than sprawling horizontally, these warehouses are being built vertically, with multiple floors of storage and operational space. This trend is particularly common in areas with high real estate demand, such as metropolitan centers.
While multi-story warehouses maximize limited land space, they also bring additional challenges and costs. The structural requirements for multi-story buildings are more complex, requiring reinforced floors and specialized systems for goods movement between floors, such as elevators, escalators, or conveyors.
3. Warehouse Automation and Robotics
Automation has become a game-changer in the warehouse sector, with advanced technologies such as robots, drones, and automated storage and retrieval systems (AS/RS) transforming the way warehouses operate. The implementation of automation requires a significant upfront investment in both equipment and infrastructure.
Automated systems can streamline operations, improve efficiency, and reduce labor costs over time, but the cost of integrating such technologies into a warehouse design can significantly increase the overall construction cost. For instance, building specialized loading docks, equipment storage areas, and control centers for automated systems all contribute to higher expenses.
4. Sustainability and Green Building Practices
As companies and governments increasingly focus on sustainability, the demand for environmentally friendly warehouses is on the rise. Many businesses are opting for “green” warehouses that adhere to sustainability certifications such as LEED (Leadership in Energy and Environmental Design). These warehouses are designed to minimize their carbon footprint, reduce energy consumption, and promote the use of renewable resources.
The implementation of green building practices involves the use of eco-friendly materials, energy-efficient systems, and waste reduction measures. While these practices can drive up initial construction costs, they often lead to long-term savings through reduced operational expenses, such as lower energy bills and fewer maintenance needs.
5. Supply Chain Disruptions and Cost Volatility
In recent years, the construction industry has faced significant disruptions in global supply chains. The COVID-19 pandemic, for example, caused major delays in the delivery of materials and increased prices for construction inputs. Shortages of key materials like steel and lumber led to higher prices, making it more expensive to build large warehouses.
These disruptions are not expected to disappear overnight, and they will continue to affect construction costs in the foreseeable future. Contractors and developers need to carefully monitor supply chain trends and adjust their budgets accordingly to account for potential cost fluctuations.
6. Labor Shortages and Increased Wages
Labor shortages have also affected warehouse construction projects. As demand for skilled labor in the construction industry grows, wages for construction workers have risen. This trend is particularly pronounced in areas with high construction activity, where competition for skilled workers is fierce.
Labor shortages can lead to project delays, which can increase costs due to the extended construction timeline. Furthermore, labor-intensive tasks such as site preparation, foundation work, and the installation of specialized systems require additional manpower, driving up overall costs.
Key Considerations for Developers and Builders
Given the rising costs and complex factors influencing warehouse construction, developers and builders need to consider several key aspects before embarking on a large warehouse project.
1. Thorough Site Analysis
A comprehensive site analysis is crucial for understanding the conditions of the land where the warehouse will be built. This includes examining the topography, soil quality, and proximity to transportation networks such as highways, ports, and airports. Understanding these factors can help developers anticipate potential issues and adjust their budgets accordingly.
2. Early Integration of Technology
Incorporating automation and other advanced technologies early in the design phase can help ensure that the warehouse is built to accommodate these systems. The earlier these technologies are integrated, the more cost-effective the project will be. Retrofitting a warehouse to include automation after construction can be much more expensive.
3. Focus on Long-Term Sustainability
Investing in sustainable building practices is increasingly seen as a wise long-term strategy. While the initial costs may be higher, green warehouses offer operational cost savings and provide businesses with a competitive edge in an environmentally conscious market. Moreover, sustainable buildings tend to have higher occupancy rates and longer lifespans, making them a good investment over time.
4. Flexible Design and Scalability
Warehouse demand can change rapidly depending on market conditions, and businesses must be prepared for the possibility of growth. Designing warehouses with flexibility and scalability in mind ensures that they can be easily adapted or expanded as business needs evolve. For example, modular designs or the inclusion of additional floors can accommodate growth without the need for extensive reconstruction.
5. Budget for Contingencies
Given the unpredictability of construction costs due to supply chain disruptions, labor shortages, and material price volatility, it’s essential to include contingency funds in the project budget. These funds can help cover unexpected costs and ensure that the project remains on track, even when issues arise.
Contact Information
Company Name: Procurement Resource
Contact Person: Leo Frank
Email: sales@procurementresource.com
Location: 30 North Gould Street, Sheridan, WY 82801, USA
Phone:
UK: +44 7537171117
USA: +1 307 363 1045
Asia-Pacific (APAC): +91 8850629517