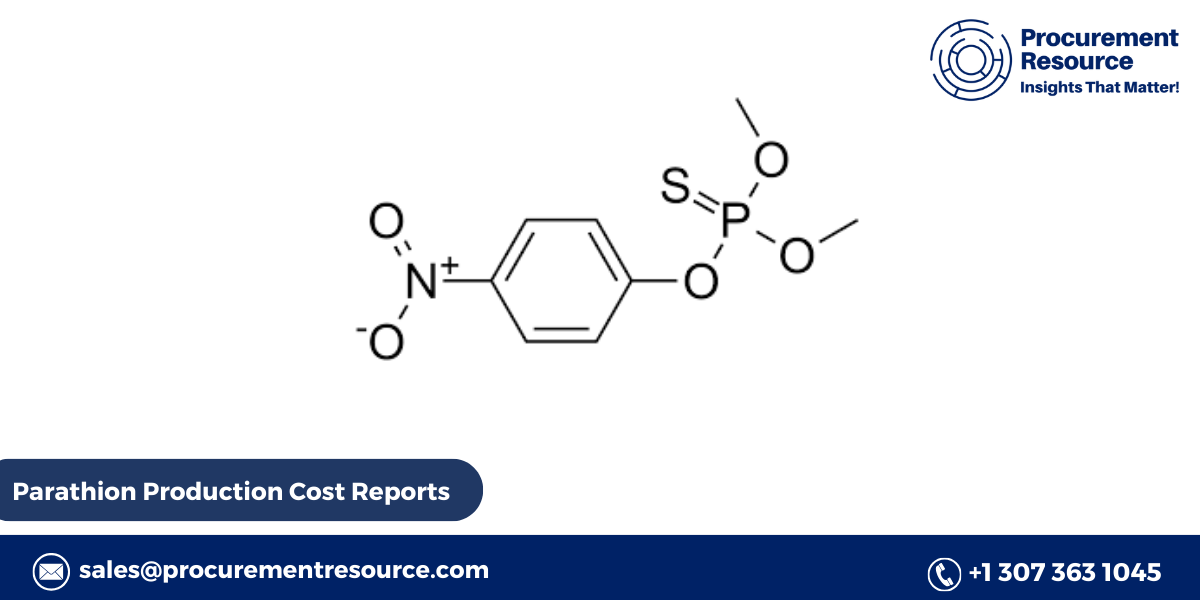
Parathion, an organophosphate pesticide, is widely used in agriculture to control a variety of pests. It is highly effective but poses significant risks to human health and the environment due to its toxicity. Despite its hazardous nature, parathion production continues, especially in countries with high agricultural outputs. Understanding the production process, raw material requirements, and associated costs is crucial for stakeholders involved in the agricultural chemical industry. This report delves into the production costs of Parathion, highlighting the manufacturing process, raw materials used, and recent industry developments.
Production Process
The production of Parathion involves a complex chemical synthesis process. Primarily, Parathion is synthesized through the reaction of O,O-diethylthiophosphoric acid chloride (DETC) with sodium para-nitrophenoxide. This process takes place in specialized chemical plants equipped to handle the hazardous nature of the compounds involved.
Here’s a breakdown of the key steps in the production process:
Request For Sample: https://www.procurementresource.com/production-cost-report-store/parathion/request-sample
- Synthesis of O,O-diethylthiophosphoric acid chloride (DETC):
The process begins with the production of DETC, a crucial intermediate compound. DETC is synthesized by reacting phosphorus trichloride (PCl3) with ethanol under controlled conditions. The resulting product is used in the next step to create Parathion. - Formation of Sodium Para-Nitrophenoxide:
This involves the reaction of para-nitrophenol (PNP) with sodium hydroxide (NaOH), which yields sodium para-nitrophenoxide. This compound is highly reactive and needs to be handled carefully to prevent unwanted side reactions. - Parathion Synthesis:
In the final step, O,O-diethylthiophosphoric acid chloride (DETC) reacts with sodium para-nitrophenoxide in a carefully monitored environment. This reaction produces Parathion and releases by-products like sodium chloride (NaCl) and hydrogen chloride (HCl). The crude Parathion is then purified to ensure it meets quality standards before being packaged for distribution. - Quality Control and Packaging:
After the production process, Parathion undergoes rigorous quality checks to ensure its purity and effectiveness. Due to its high toxicity, Parathion must be packaged and stored in compliance with safety regulations to avoid accidental exposure.
Manufacturing Report and Process
Manufacturing Parathion requires sophisticated facilities with a focus on safety and environmental compliance due to the highly toxic nature of the chemicals involved. Below is a detailed account of the manufacturing report, highlighting the key components of the process:
- Infrastructure and Equipment:
Specialized reactors and distillation units are required to handle the chemical reactions and purify the Parathion product. These reactors must be corrosion-resistant and capable of operating under controlled temperature and pressure conditions to prevent the formation of unwanted by-products. - Skilled Workforce:
The production process requires skilled chemists and engineers familiar with handling hazardous materials. Continuous monitoring of the process is necessary to prevent accidents and ensure the efficiency of the production. - Regulatory Compliance:
Since Parathion is a hazardous material, manufacturing facilities must comply with stringent regulations regarding worker safety, environmental protection, and waste disposal. These include measures to contain emissions of harmful gases like hydrogen chloride (HCl) and the proper treatment of any liquid waste produced during the process. - Waste Management:
The by-products of the Parathion production process, such as sodium chloride (NaCl) and hydrogen chloride (HCl), require proper disposal or recycling to minimize environmental impact. The manufacturing facilities must have appropriate waste management systems in place to handle these by-products safely.
Raw Material Costs
The primary raw materials required for Parathion production include:
- Phosphorus Trichloride (PCl3):
A key component in producing O,O-diethylthiophosphoric acid chloride (DETC), phosphorus trichloride is a significant cost driver in the production process. Fluctuations in the price of phosphorus, driven by demand in other sectors like fertilizer production, can impact overall production costs. - Ethanol:
Ethanol is used in the synthesis of DETC. The cost of ethanol is subject to volatility, particularly due to its role as a biofuel. Global trends in energy markets can directly affect the cost of ethanol, and thus, Parathion production. - Para-Nitrophenol (PNP):
Para-nitrophenol is another essential raw material in Parathion production. Its price is influenced by demand in the chemical industry and availability from suppliers. Any disruption in the supply chain, such as environmental regulations or trade restrictions, could lead to price hikes. - Sodium Hydroxide (NaOH):
Commonly known as caustic soda, sodium hydroxide is used to convert para-nitrophenol into sodium para-nitrophenoxide. While its cost remains relatively stable, any changes in the chemical industry could have downstream effects on the overall production costs of Parathion.
The overall cost of Parathion production is highly dependent on the availability and prices of these raw materials. Price volatility, driven by global supply-demand dynamics, is a key consideration for manufacturers.
Latest News
In recent years, there has been increasing scrutiny of organophosphate pesticides like Parathion due to their environmental and health impacts. Several countries have imposed strict regulations or outright bans on Parathion usage, particularly in food production. This has resulted in a decline in Parathion demand in regions like Europe and North America. However, Parathion production continues in developing nations with high agricultural outputs where regulatory frameworks are less stringent.
Key developments in the Parathion market include:
- Shift Towards Alternative Pesticides:
With growing awareness of the environmental and health risks associated with Parathion, many countries are transitioning to safer, less toxic alternatives. This trend is expected to continue, with the market for biological and environmentally friendly pesticides gaining traction. - Impact of Trade Regulations:
The global pesticide industry is subject to numerous trade restrictions, which can affect the production and export of Parathion. Countries with stringent pesticide residue limits in food exports are likely to phase out Parathion in favor of more acceptable options, affecting global demand. - Technological Advances:
Some companies are investing in research to develop more efficient Parathion production processes that reduce waste and minimize environmental impact. Innovations in chemical engineering could potentially lower production costs while enhancing safety measures. - Environmental and Health Concerns:
The toxic nature of Parathion has led to widespread concerns over its environmental persistence and potential health hazards. This has prompted increased regulation, which is likely to impact both production volumes and prices in the coming years.
Contact Us:
Company Name: Procurement Resource
Contact Person: Endru Smith
Email: sales@procurementresource.com
Toll-Free Number: USA & Canada - Phone no: +1 307 363 1045 | UK - Phone no: +44 7537 132103 | Asia-Pacific (APAC) - Phone no: +91 1203185500
Address: 30 North Gould Street, Sheridan, WY 82801, USA
Website: https://www.procurementresource.com/